Cold
has become decidedly cooler at Frankfurt cargo. Europe’s largest
airline hub for temperature-sensitive shipping has grown even more high,
wide, and handsome, after a significant expansion and upgrade at The Lufthansa
Cargo Cool Center (LCCC).
Hard on the heels of holding its annual
press conference, where the expected announcement of a bounce back year
in 2017 came through with flying colors, the LCCC has just completed an
overhaul that includes a footprint expansion to over 8,000 square meters,
almost doubling itself.
It is no surprise that LCCC was put on
the half shell as part of an expanded press tour.
Lufthansa Cargo, in a sentence, is back
and hitting many of the right notes that have traditionally made the cargo
enterprise the class act and innovator of the air cargo world.
Numbers
& A Cabin In The Sky
Thursday, March 23 was numbers day at Lufthansa Cargo, a time when
the Frankfurt, Germany cargo carrier dares to fly a route that few other
air companies travel, outing their yearly performance numbers to the working
press, and then sticking their chins daring:
“Hit
me with your best shot.”
We are gathered
in a gleaming metal room with a curved hangar like roof on the fifth floor
of the Lufthansa Aviation Center at Frankfurt International Airport.
The venue,
a cabin in the sky, features a floor to ceiling window wall that looks
out on a ground control tower and the runway. The building is on a street
named for Dr. Hugo Eckener, the legendary German visionary, manager of
the Luftschiffbau Zeppelin during the inter-war years, and also the commander
of the famous Graf Zeppelin.
Across the
street aircraft are moving about, coming and going at the big airport;
airplanes passing by, some from destinations that are familiar, to other
places yet to be discovered.
Inside is
a sanctuary with the passing scene as backdrop.
There is a
touch and feel of welcome here in this bright room with its spiral staircase
leading upward to another floor where the top executive of the entire
airline, Carsten Spohr, has his office.
Change Is
In The Air
Lufthansa
is a changing airline.
In summer,
this bright glorious room serves as play center for children that accompany
their parents to work during their summer vacation.
There is something
reassuring about transforming a space once given to graphs, powerpoints
and big ideas into finger paints, balloons and nap time, perhaps even
stories from Uncle Martin (Lufthansa Cargo CFO).
Last year
as 2016 numbers came in and the red ink flowed, word up was that things
might get worse before they got better.
Here in 2018,
the message was completely reversed as the numbers delivered by Lufthansa
Cargo were not only up, they fairly blew the roof off the top of the hangar.
Wrong Is All Right
An effusive
Peter Gerber, CEO and Chairman of the Executive Board of Lufthansa Cargo
AG opened his remarks proclaiming:
“I was
wrong.
“In
2017 when we met at our yearly event I predicted a continued downtrend
but that was completely turned around beginning last September.”
Now with results
in hand, Mr. Gerber beamed, that last year delivered, ”one of the
most successful years in the history of Lufthansa Cargo.”
Number One
In The World
“Today,”
Peter Gerber exclaimed, “Lufthansa Group yield is number one in
the world.
“In
2017 sales of Lufthansa Cargo rose by 21.1%,” Peter Gerber said.
“Our
team is highly professional and passionate.
“We
will continue to focus on our efficiency program, investing in our ground
infrastructure, special business initiatives and digitization,”
he declared.
On Top Of
The World
Dr. Martin
Schmitt, Lufthansa Cargo CFO further underscored Mr. Gerber’s words:
“We
feel like we're back on top of the industry.
“Demand
and utilization have significantly improved and raised our load factor
whilst unit costs remained steady and revenue went from 16.7% to 19.6%.
“In
2017,” Doc. Martin said, “our volume rose 6% while yields
delivered at 14% uptick.”
Peter Gerber
adds, “We have worked top to bottom as a company to turn things
around.”
Taking Nothing For Granted
“I cannot
say,” Peter Gerber declared, “that without some luck and good
timing we would be positioned as Lufthansa Cargo is today, but we are
certainly not taking anything for granted.
“Lufthansa
Cargo moving forward will deepen our partnerships, enhance customer connectivity,
continue to automate our processes and develop new business models for
the digital culture.”
Mercedes
Of Air Cargo
During a walkabout
inside the colossus called Lufthansa Cargo Cool Center, one notices right
away that this very busy, giant layout of container-filled rooms hums
along, smooth and confident in a place loaded with high-tech cool chain
solutions.
Today Lufthansa is the Mercedes of air
cargo—powerful, confident, and filled with promise.
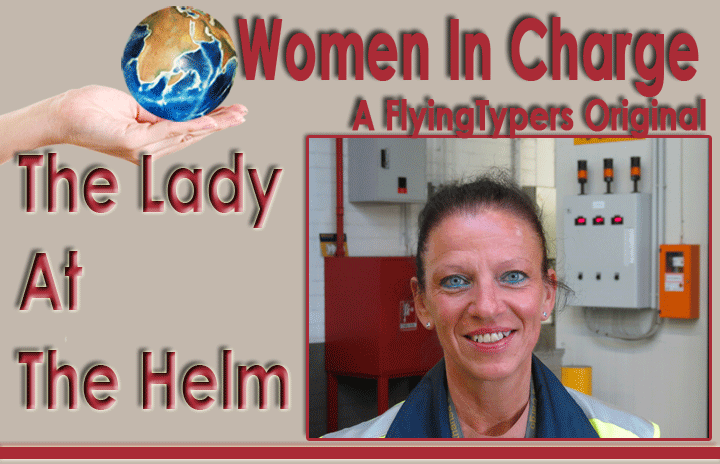 |
We
spoke to Karin Krestan, Head of the Lufthansa Cargo Cool Center.
Karen is the energetic and engaging boss
of all things temperature sensitive.
She is not a late arrival to the cool-chain
party, but in fact has been a driving force shepherding the Lufthansa
Cargo Cool Center since it opened in 2011.
Armed with a keen working knowledge of
how the cool-chain must be handled, Karin oversees a 24/7 ballet—moving
everything from the pharma and healthcare business through giant electric
doors to aircraft waiting outside on the ramp.
After spending an hour with this most professional
lady, we kept thinking about how Karin’s expertise, balance, communication
skills, and sense of humor fit perfectly into the age of the digitally
driven, increasingly transparent cool chain.
For one thing, she keeps things simple.
Cool
From The Ground Up
“Lufthansa has a
vast menu of service offerings for pharmaceuticals, diagnostics, clinical
trials, biotechnological material as well as temperature-sensitive, high-tech
products, including temperature-controlled ground storage,” Karin
said.
“However, we are a ground-up cool-chain
with appropriate cooling facilities, including our dedicated Cool Center
operations here at our hub, Frankfurt, and also in other key locations
around the world.
“We offer temperature ranges per
compartment onboard the aircraft and on temperature-controlled reefer
trucks for our road feeder services.”
Lufthansa
Driving Firsts
“We are the world's first cargo airline to offer their customers
the “Road Feeder Service Cool” (RFS-Cool) booking option.
The new service ensures that temperature-sensitive cargo is actively or
passively cooled or warmed, not just on board aircraft, but also in road
link connections where similarly equipped vehicles are set up.
“Customers
can make through shipping arrangements within Europe on the new “Road
Feeder Service Cool” for sensitive medication that has been flown
into Frankfurt and ensure that the goods remain inside the specified temperature
range on the intra-Europe segment of the journey.
Innovation
Is Constant “Our
innovative cool-chain solutions include transit points at Lufthansa’s
hubs at Frankfurt, Munich, and Vienna with a variety of containers that
offer specific services.
“The Lufthansa Cargo Cool Center
is equipped with state-of-the-art cool storage rooms for four different
temperature ranges, exclusive ramps for delivery and goods acceptance,
an exclusive Competence Center Temperature Control (CCTC) supervision
team on call 24/7.
Located
Within Security Hub
“Another advantage
is that our pharma-zone cool-chain solution at Frankfurt is located within
the security hub and has direct access to the apron. This guarantees shortest
distance transfer and minimizes cross-transfer between different facilities.”
Pharma
& Love Of A Nurse
Karin Krestan began her
career at Lufthansa working on the passenger side, but before long her
professional training as a medical nurse took hold and after reading about
the Cool Competence Center in 2007, Karin was immediately fascinated at
the possibilities of bringing her firsthand knowledge of pharma and vaccines,
plasma etc. to work, building the Lufthansa offering while still located
at PCF.
“I discovered right away that the
pharmaceutical industry very much likes talking to someone who has working
knowledge and understanding of the medical arts in matters, such as special
sensitivity requirements of certain pharma products: for example, how
to handle insulin.”
Development
Is Ongoing
“We are quite
accomplished in our business here but are still at work improving our
offering, including product development and continually refining features
to better serve our customers.
“We also hold meetings that are conducted
both internally amongst our team members and externally with our customers
to develop the best systems and practices that interface via computer
with shippers.
“But it is most important that
we offer constancy—i.e., staying away from critical situations associated
with any fluctuation in temperature for the goods we move through here.
“Keeping things on a steady beam
requires constant monitoring, which we do at a special 24/7 desk that
offers temperature monitoring and mapping.
“Customers can track much of the
same information about their shipments including current conditions and
delivery schedules.
“This two-way contact keeps everybody
on the same page with complete transparency and no surprises.
“We are also quite proactive in getting
the word to our customers at once if a delay or something else occurs.”
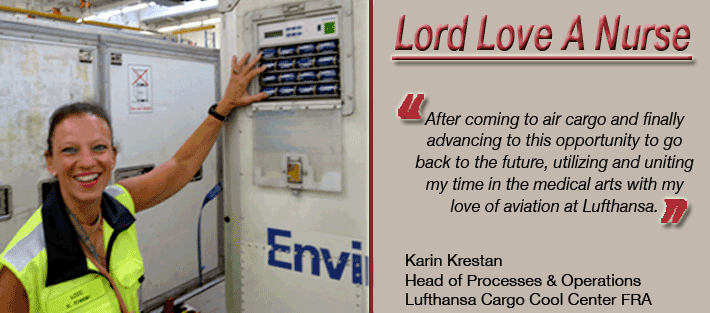 |
From
Nurse to The Cool Center
We wonder about Karin’s
journey to become a nurse, recalling that at one time back in the early
1920s, all flight attendants serving aboard line aircraft in America were
nurses.
This was at a time when the ride aboard,
say, a Ford Tri-Motor could get rough enough to warrant medical attention.
“I worked in the local hospital in
Darmstadt as a nurse’s aide during my student years.
“I just got used to the work and
liked the interaction with the patients, how the hospital operated, and
I guess I never forgot that time.
“I spent three years working in the
Emergency Room, where the real action is.
“Then a close friend was hired as
a flight attendant at Lufthansa and I thought that working for this airline
would be an interesting career.
Started
On The Ramp
“But having just given birth to my
first child, working aboard aircraft and travelling would not have worked,
so I was hired here to work on the ramp.
“After a few years on the passenger
side, I moved to the Lufthansa training center in Seeheim, where I then
began teaching what I had learned.”
Brave
New World
“One of the more
interesting aspects of teaching at Seeheim is the opportunity to attend
any of the classes offered there, including training on how to be a station
manager for Lufthansa anywhere in the world.
“From that training I was able to
work as a replacement manager in some interesting stations, including
Kenya and Russia, before finally making my move to Lufthansa Cargo as
head of aircraft handling.
“After going to air cargo there was
one more move to the passenger side before finally advancing to this opportunity
to go back to the future, utilizing and uniting my time in the medical
arts with my love of aviation at Lufthansa.
Looking
Ahead
“So things
have gone full circle, but I really love this job.
“What we are really doing here is
creating a decent balance of the best and brightest, most dedicated people
available.
“We have 26 women in the office and
45 men in the operations part of our cargo operation here. All of our
people contribute and are very dedicated to their work building Lufthansa
Cargo Cool Center,” Karin Krestan said.
As we leave this most interesting part
of the Lufthansa Cargo combine at Frankfurt Airport, a sticker that my
Mother used to feature on the rear bumper of her VW Golf comes to mind:
“Lord Love A Nurse,” it said.
Now that we know one, we understand why.
Geoffrey |