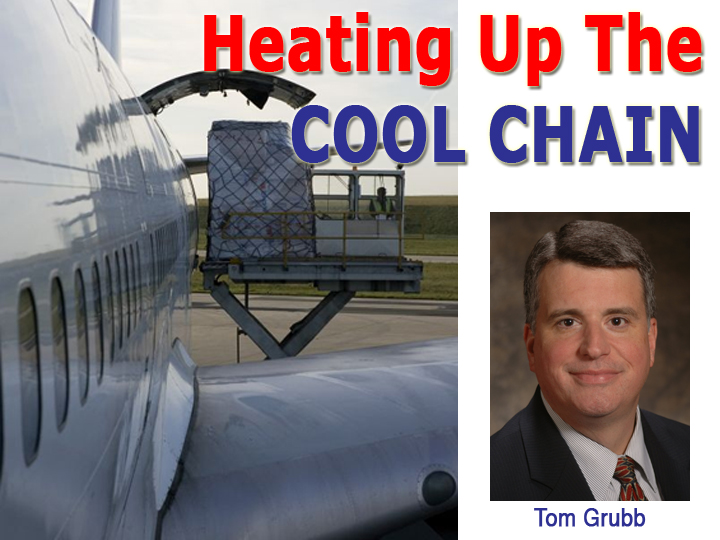
First of all, you have
to love the classical overtones.
Tom Grubb, manager, Cold Chain Strategy
at American Airlines, knows a lot about what he does, and like any true
devotee he loves his work and makes no secret of it!
“The air cargo cold chain is like
a symphony orchestra, with many performers playing in harmony as a cohesive
group.
“Seamlessly playing as one not only
demands professionals skilled in their respective instruments; it is also
requires that all participants read from the same score.
“In the pharmaceutical cold chain,
safely and effectively moving time- and temperature-sensitive products
means all stakeholders need to follow the same standards, regulations,
and best practices.”
Tom actually told us that a couple years
ago and it caught our attention. People who take joy in their work touch
us like that.
Fast forward to 2015 and Tom once again
assures that at AA Cargo, the heat is on cool chain solutions.
“American is poised for added growth.
“We just opened a dedicated, state-of-the-art
Pharmaceutical & Healthcare handling facility at the Philadelphia
International Airport.
“The facility has significant capacity
for Controlled Room Temperature (CRT: +15°C to +25°C) as well
as a refrigerated cold room (COL: +2°C to +8°C).
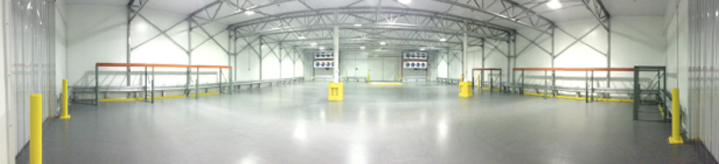
CRT: +15°C to +25°C
“There is a dedicated active container
management (ACM) area with plug-in stations for up to 30 equivalent RKN
electronic-type units and the facility has an independent power backup
system.
“American’s commitment to cold
chain is shown in the numerous enhancements we have made to many of American’s
facilities across our network.
“This is crucial to insure we continue
to meet and exceed the expectations of customers.
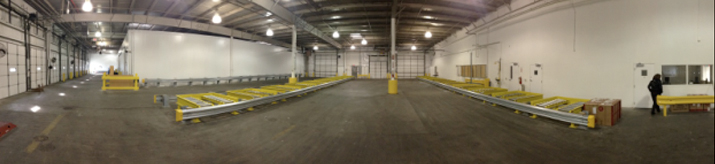
Active Container Management (ACM), Front Dock
Learning
Develops Significant Benefits
“American Airlines Cargo has gained
significant experience with temperature control, since launching its “ExpediteTC°
services over 5 years ago.
“We began with ground-up development
of our Active services and, after some experience with Active, we developed
our Passive service offering.
“We continue to invest in our ExpediteTC°
program in terms of process evaluation, program features, and infrastructure—including
implementation of Controlled Room Temperature (CRT +15°C to +25°C)
facilities in key stations across our network.
“This also includes a brand new, dedicated
pharmaceutical & healthcare handling facility.
“We were one of the very first air
carriers to implement annual recurrent training for all our employees
responsible for temperature-controlled shipments and this extends to our
ground-handling partners.
“We are currently working on new training
tools this year to insure the very best cold chain understanding for our
employees.
“This way, they can provide the very
best service for our customers.
“Most importantly, when it comes to
temperature-sensitive programs, is understanding customer needs and how
their products change over time.
“In this way, we will continue to
update American’s solutions in order to meet customer and product
requirements.”
Tom Terrific
As Manager of Cold Chain Strategy, Grubb
leads global time and temperature sensitive logistics services for American
Airlines Cargo. A 23-year veteran of American’s Cargo division,
Grubb previously served in Operations as manager of Customer Service Strategy,
where he was pivotal in the development of American’s Active and
Passive cold chain services, ExpediteTC. During his tenure with American
Airlines Cargo, he has implemented strategic sales initiatives as well
as operational solutions for American’s product and services portfolio.
Mr. Grubb is currently a member of the IATA
Time and Temperature Task Force (TTTF).
Today & Tomorrow
“American continues to see solid growth
of our temperature-sensitive pharmaceutical and healthcare business in
2014. Product complexities, as well as increasingly stringent regulatory
requirements, contribute to the growing need for specialized supply chain
solutions, which keep medicines safe and effective for patients.
“American’s temperature-controlled
solution provides the features desired by customers and we continue to
enhance and evolve the program with added benefits, which pharmaceutical
manufacturers and freight forwarders indicate are requisite for properly
handling these materials.
“Our vast network capability is coupled
with the robust and reliable processes built into ExpediteTC°, which
are designed to protect delicate healthcare shipments.
“This is complemented by the recent
roll-out of the ExpediteTC° process across the American Airlines’
extended network following our merger with US Airways. Philadelphia, for
example, is a prime location in the heart of the U.S. pharmaceutical corridor
which, when coupled with the world’s largest airline, provides temperature-controlled
cargo capability to/from Europe, Latin America, and the Pacific.
“Our ExpediteTC program is designed
strictly for the pharma and healthcare sectors.
“This is critical given the regulatory
requirements for separation of pharmaceuticals and foodstuffs to avoid
cross-contamination. That said, American also has an excellent perishables
program which can certainly assist any customers with their flowers, produce,
fish, etc.”
Cool-Chain Closer Look
“As an industry, I think we are all
working very diligently to address the concerns with all modes of transportation.
“Given that airport operational environments
can be very challenging, it is critical that solutions like ExpediteTC°
are implemented, evaluated from a quality perspective, and refined to
insure maximum protection for these delicate products.
“Pharmaceutical manufacturers, forwarders,
air carriers, and all members of the temperature-controlled supply chain
must address these requirements by working together.
“In addition to the needed training,
processes, and infrastructure, a key imperative is that all supply chain
participants need to be informed and aware of as well as adapt to changing
temperature-sensitive regulations, particularly due to the fact that pharmaceutical
distribution standards are not universal.
“As an example, the EU’s Good
Distribution Practices (GDP) quality assurance guidelines have certainly
been the focus of much discussion in the past few years, but so too are
the regulations from U.S. Pharmacopeia (USP), the U.S. Food and Drug Administration
(FDA), and the UK’s Medicines and Healthcare products Regulatory
Agency (MHRA), etc. as examples.
“Each of these can have differing
perspectives and this also extends to individual countries’ customs
authorities. It is these complexities which are helping to drive growth
and rapid change in the temperature-controlled supply chain, as well as
the need for enhanced collaboration between all participants.”
Talking containers here wondering if you
are thinking as a former ops guy about cool-chain containers of today
and tomorrow? What for example does the pharma container do today and
what looking ahead do you think will be the container of tomorrow?
The newer, electronic units of today are
easier to maintain, rechargeable, maintain more accurate temperature ranges,
etc. as compared to the dry ice variants developed in the late 1990s which
are still in use today. With the tighter restrictions on temperature control,
I would expect you will see vendors working on continuing improvement
of accurate temperature maintenance capabilities but also perhaps the
reduction in the size/weight of these mechanisms, technology permitting.
Currently, the systems required are not small and therefore take up payload
capacity. Perhaps in the future, these mechanisms can be reduced in size
and enable better temp control with less weight and bulk. Also,
the ability to have more “real-time” communication with the
units including product temperature and unit status is becoming much more
desirable as delicate products move through the supply chain. This is
happening today but still there is much room for added capabilities as
monitoring requirements increase.
Geoffrey/Flossie
|