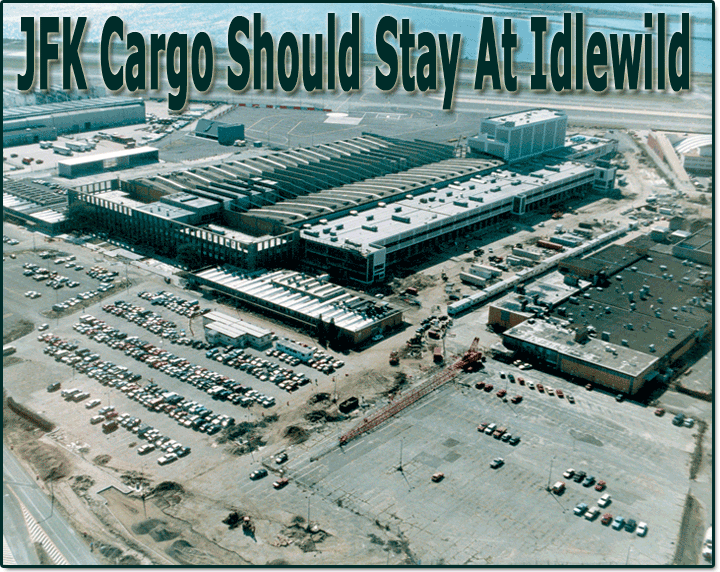
There is a plan being floated by New York
State to move all air cargo action from JFK International Airport (located
in the Borough of Queens, at a place once called Idlewild), to a sleepy
upstate country location called Stewart International Airport, 60 miles
north of Gotham.
In 1978, while out riding in a car together,
I asked my good friends, the late former Port Authority of NY & NJ
Aviation Director Caesar B. “Pat” Pattarini, and the late,
great General Manager of JFK (retired in 1984) Ike Dornfeld, (right) if
they thought moving cargo to Stewart was a good idea. Both laughed out
loud.
Well, what goes around comes around; once again,
Stewart is in the headlines—although as the idea was floated by
politicians around election time, we can only wonder if it has any legs.
Prior to 9/11, Stewart International Airport
handled as much as 100,000 tons of air cargo annually and had a growing
passenger business built on narrow-body commercial service.
The NYS Department of Transportation, which then
controlled the airport, saw the activity levels as potentially attractive
for private investment. In 2000, DOT privatized the airport: the National
Express Group (NEG) of the UK assumed control with a 99-year lease and
the belief that their marketing efforts and business acumen would grow
the operations. Relationships with the surrounding community were contentious
and airlines focusing on their profit margins pulled out of Stewart.
In 2007, NEG opted out of the contract and the
Port Authority of New York and New Jersey purchased the lease with a major
commitment to invest in and develop the airport’s business. This
year, Stewart stands as a prime example of changing industry dynamics,
and despite the best efforts of the PA, will handle about 20,000 tons
of cargo—down 80 percent in the past decade.
The air cargo segment of the aviation industry
is in many ways far more complex than the passenger side of the business.
However, one thing that both segments have in
common is a focus on the bottom line.
Cargo is particularly sensitive because of the
competitive nature of the business, very low yields, and tight profit
margins.
An airline is not an economic development tool:
it is a business that must make measured and sometimes difficult decisions
that impact the markets it serves and the stakeholders it represents.
When evaluating the viability of a cargo operation
for an airport, we examine 25 factors in three broad categories: Industry
Variables, Business Partners, and Factors for Success.
A quick review parallels the industry’s
perception that to serve New York, there are better options than Stewart.
No laughter yet, but on a measured and calm basis
let’s consider the proposed relocation from the perspective of the
three “C’s” that drive cargo – Connectivity, Consolidation,
and Costs.
Connectivity
The success of an air cargo operation is predicated
upon an effective system of connective elements that enable aircraft to
balance inbound and outbound tonnage in volumes sufficient to make a round-trip
flight profitable and affordable for their customers. Cargo may be destined
to move from A to B, but that does not preclude stops at C and D, or the
utilization of a circle route between several points to generate adequate
cargo volumes.
This often involves connections between different
carriers or “interlining” and requires a strong multi-option
support system on the ground as well as in the air. Redundant air options
are also critical for international shipping and these are most often
available in the bellies of passenger aircraft.
Stewart offers virtually no connectivity and
JFK has the most diverse connections in the Northeast.
Last year JFK had more than 400,000 aircraft
movements to over 100 domestic and international destinations.
Consolidation
Air cargo is a high-volume, low-margin business
whose success depends on serving diverse markets, filling outbound airplanes
with large volumes of cargo, and bringing the planes back equally full.
This requires both diversity and volume in the
distribution system and takes close coordination among many partners in
the logistics chain. Cargo routes must be built block-by-block until together
they begin to offer sufficient lift to attract and ship new cargo at reasonable
rates. As different routes/customers are added, the incremental volumes
they bring create a self-fulfilling prophecy—“more volume
creates more lift, which lowers cost, which attracts more volume.”
In 2014, JFK will handle about 1.4 million tons
of cargo compared to about 20,000 tons for Stewart.
The savings generated by the economies of scale
are significant.
Costs
The ability to ship quickly anywhere in the world
is important, as is the ability to build sufficient freight volumes to
sustain a cargo operation.
But the key is cost.
Connectivity by ground or air keeps freight from
sitting and adding additional costs to the logistics supply chain.
Through consolidating volumes, the industry evaluates
the viability of a given route because the greater the volume, the lower
the per-pound shipping cost, and the higher the profitability. For an
airport to be successful, the industry must believe that the three “C’s”
are clearly in play and that they bring direct benefit to the carriers.
Despite the perceived “cost of doing business”
in New York City, the cost of per pound shipping and reduced trucking
time to the core of the City offset higher operating costs at JFK.
When looking at the numbers, it’s important
to remember that only about 50 percent of JFK’s cargo is destined
for the immediate region. The rest comes and goes from all over the country,
from points as far west as Seattle and as far south as Miami. In 2025,
forecasts predict that JFK will handle about 2.5 million tons of cargo.
Of that, about 530,000 tons is domestic.
The tonnage on the passenger flights will not
move because the passenger flights will not move.
The freighter traffic is almost entirely integrators,
whose business model requires that they be as close as possible to the
central business district.
Roughly 800,000 tons will be international belly
cargo, which will stay where it is because the passenger aircraft will
not move.
That leaves roughly 1.1 million tons of international
freighter traffic—about three quarters of that tonnage is flown
by carriers who also fly passengers into JFK. History tells us that they
will be very much opposed to splitting an operation and in effect incurring
double costs.
That leaves approximately 300,000 tons that is
flown by carriers that need to connect to other carriers and a broad ground
transportation network that covers most of North America.
For them, relocation to an airport without those
connections is not an option.
The fact of the matter is that for the past ten
years carriers and all the supporting air cargo businesses have had a
“Stewart Option,” and have declined to move there because
it is inconsistent with their business model, and would be disruptive
to the massive and intricate ground distribution network that involves
hundreds of firms on both the shipping and receiving ends.
Operating from JFK is not a question of arbitrary
preference; it represents sound business decisions that consider how best
to provide service, maintain profitability, and control costs for their
customers and business partners.
A Postscript
But Pat and Ike told me most of this (minus the
2014 updates, obviously) a long time ago.
I can therefore only share a lesson learned,
something I have thought about and believed for all these years.
I still think about those guys and Tim Peirce
over at LaGuardia, and Vince Bonaventura at Newark International.
I loved ‘em all and still do, and I’m
proud to be part of the New York airport scene having moved forward during
the past 44 years.
New York State politicians need to keep their
mitts off of JFK International Cargo, except to invest more state funds,
raise the quality of access, and add other necessary, valuable abilities
to an airport that serves the greatest city in the world.
Geoffrey |