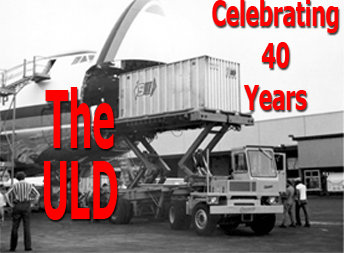 |
|
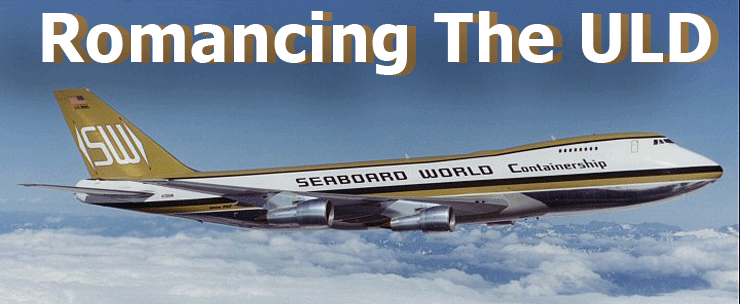
You might think
we have gone a bit soft in the head to devote real estate in this highly
professional publication to such a decidedly unglamorous article of
airline lifecycle! It’s kind of like the joke with the various
body parts competing for primacy, and you’ll never guess who wins
… right!
Then think again - we mark the launch
of the first commercial 747 flights - the evolution of the ULD (unit
load device) era-changing forever the way in which airfreight and baggage
was handled. The first Pan Am Boeing 747 was put into service on January
15, 1970, although it seems the first flights regularly carrying fare-paying
passengers only started on January 21.
Either way, we have had 40 years
of ULDs as an essential part of commercial widebody air travel, truly
the link in the air cargo supply chain that changed everything. We have
come a long way in those four decades with ULDs becoming ever lighter
and stronger, as well as becoming more versatile while specialized,
indispensable for the proper handling of all types of cargo and baggage.
Many people have taken it for granted
due to the ubiquitous nature of the lowly ULD. Yet, no ULDs, and the
passengers’ baggage ends up being left behind with predictable
customer service failures or it is bulk loaded and unloaded, which negatively
affects ground time and service. No ULD and that newly won hot account’s
first must-ride shipment is backlogged. And so this relatively insignificant
piece of equipment all of a sudden gets much attention, but no love.
Just to make sure
we are on the same page – at the risk of stating a known fact,
legally, ULDs are ‘ship spares’ subject to the very same
aeronautical regulations as the aircraft itself. This extends to airworthiness
and certified manufacturers and repair facilities. Although clearly
critical from an operational perspective, in the big scheme of things,
ULDs don’t rate high in terms of executive attention and budget,
unless – you got it - there is a service failure that stinks to
heavens – think fish!
Airlines and the industry insist
that safety is the first order of business, yet from aircraft manufacturers
to airlines, money has been spent on passenger convenience items such
as video screens in seatbacks, but nothing has been invested to have
automatic identification readers onboard to confirm units are loaded
according to the load plan, whether top side or in the lower deck on
wide body aircraft.
Leaving the development and implementation
of such solutions to the after-market arena saddles any potential innovator
with the enormous burden of obtaining certification for non-interference
with avionics and the nightmare of available frequencies.
Not an attractive proposition in the best of times and, needless to
say, a very tall mountain to climb in a tough economic climate.
Cross-discipline standardization is perhaps
the biggest cause of unmet potential simplification and its economic
benefits.
Let’s review briefly how it
all evolved. Before the advent of wide body aircraft, all-cargo airlines
used ULDs - from the ubiquitous set of aluminum pallets and nets to
the igloos. First the B707, then the DC8-55F with 13 pallet positions
in 1964, followed by the legendary DC8-63F stretched freighter in 1968,
became the backbone of the cargo business, the latter carrying 90,000lbs
of freight loaded in 18 pallet positions.
This facilitated a previously unprecedented degree of efficiency and
economic viability in loading and unloading aircraft and ramp handling.
The mainstay standard pallet has been the 88” X 125” type
and cargo loaded using a template shaped as a cutout of the fuselage
to ensure fit with the aircraft contour.
There is a wealth of information
used by airlines and ground handling companies alike which contains
detailed specifications and is a must have item – the IATA ULD
Technical Manual.
This is the foundation of interoperability
among airlines worldwide. The IATA operated Interline ULD Control User
Group (IULDUG) with its roughly 60 member airlines and which –
to quote IATA - “…was formed to facilitate the interline
movements of ULDs, under standard procedures, and to track ULDs when
they are outside the control of the ULD owner.”
Setting up for loading 113 polo ponies on the main deck en-route
to Bandar Seri Begawan (Brunei), Malaysia and the Philippines. Photos
courtesy of Ted Braun.
Configured for a triple and a quad Instone horse stall across in each
stick (left; right).
The military version of the pallet
and net combo ended up as the 88 “X 108” “MAC”
pallet, designed to handle pallets with a secondary function of airdrop.
As CRAF (civil reserve air fleet) participating airlines have experienced
for years, loading this type of pallet on commercial aircraft requires
time consuming resetting of the entire floor locking mechanisms –
vertical, lateral and side locks – before and after a mission.
As documented in Air University
Review, July-August 1982, “A Uniform National Air Cargo System
Do we need it?” by Paul D. Tuck which states “If unit-load
devices were fully interchangeable between civil and military aircraft,
the total number of ULDs required by the two airlift systems could be
reduced”. And “…The DC-8 productivity in cargo carried
is increased about 11 percent when civil, rather than military, pallets
are used.”
Igloos came in all varieties –
with doors, curtains and “GOH” – garments on hangers,
enabling transportation of time-sensitive fashion merchandise by air.
Livestock became another commodity to be commercialized, transporting
efficiently by air breeding stock to countries, which were beginning
to build up their infrastructure in the 80’s, including Kuwait
and Saudi Arabia, all under Irish agro-management. The supply came mostly
from the U.S., Australia, Germany and the Netherlands.
By the time Lufthansa, as launch
customer for the B747-200F started flying them, and with both Seaboard
World Airlines and Flying Tigers introducing them to service in 1974,
yours truly witnessed the mind boggling 29 upper deck and 9 lower deck
positions loaded with 200,000 plus pounds of freight for simultaneous
nose and side door loading and unloading!
My jaw dropped when I saw the first
Seaboard LODEP in Frankfurt!
The Seaboard version was named the
“Containership” and pioneered the use of 20-foot equipment,
which also enabled the famed “sea-air” cargo intermodal
concept. Initially marine containers were used which carried a vey hefty
tare weight and were loaded on 20 foot pallets. Air containers made
of aluminum soon followed. This equipment could be taken off-airport
to either the freight forwarders’ or the customer’s distribution
center for loading and breakdown anchored on trucks with ISO corner
fittings. 10-foot containers or “cans” followed.
There
are approximately 60 companies worldwide engaged in ULD manufacturing
and repairs based on the IATA compatibility codes.
From the utilitarian, ULDs have
progressed to a plethora of special purpose devices – main and
lower deck, forkliftable and non-forkliftable containers, animal units
(cattle, horses, goats, and sheep), ULD for aircraft engine transport,
automobile transport (single and twin car racks) and a variety of thermal
containers.
While looking at the utilization
of ULDs in cargo, the passenger business has deployed containers throughout
the world for as many years, using an ever increasing ‘making-your-head-spin’
variety of ULDs for baggage; here is a quick overview of some of the
more frequently used lower deck containers:
Source: Wikipedia |
In the wake of
the downing of Pan Am flight 103 over Lockerbie in 1988, initial government
reactions prompted efforts to explore “bomb-proof” containers.
Trials produced equipment alleged to withstand an explosion of the magnitude
suffered by the Pan Am aircraft using various techniques, whether in
material or construction. The ‘Q’ series represents certified
hardened aircraft containers.
Aluminum ended up sharing the space
with composite materials, which made it more economical to repair damage
but weigh more. Indeed the pursuit of lightweight materials continues
to this day, well after Lexan, which is lightweight, clear and weather
resistant. I am waiting to see something, which is forklift resistant…..
The quest for innovation and for the “perfect” ULD marches
on; last year Lufthansa Cargo together with Jettainer, its ULD pooling
and management provider (partially owned by LH), tested about 1,000
composite containers made of materials that are 15% lighter than aluminum.
Additionally, their repair is alleged to be less costly while also enhancing
safety during handling. The main ingredient which delivers these advantages
is Dyneema®, whose manufacturer, DSM, claims it’s the world’s
strongest fiber which has a unique combination of strength and softness.
As fuel and “green”
are perennial economic drivers, at times in parallel, at other times
interchangeably, this seems to be one of the more promising alternatives
because the fiber has been in production for almost 20 years.
Temperature controlled ULDs have
revolutionized air cargo; from humble beginnings and primitive controls
with minimal ranges in the aircraft, nowadays high yield pharmaceuticals
and sensitive electronics travel first class, ensconced in plush, dedicated
equipment with digital readings and in-flight transmission capability
on demand. All kinds of perishables, from fresh cut flowers, to chilled
seafood, bull semen, plasma – the list is endless, have evolved
into a specialized niche of cargo products with more and more sophisticated
supply chains and shorter door-to-door transportation time.
Some of the key players in the
supply end of temperature controlled ULDs include Envirotainer and Unitpool,
two of the best known and established global players and newbies such
as Skycooler (2006), the UK-based temperature controlled container leasing
company. The latter’s management team includes Jorgen Veslov as
CEO, a former Unitpool AG manager and Philip Hill as Chairman, formerly
Unitpool’s managing director.
Considering the bi-directional
imbalance inherent in the airline business in both passenger and cargo
loads, combined with the location of certified repair stations, securing
the required stock levels throughout an airline’s network poses
a significant logistical challenge. And ULDs go off-airport to forwarders,
distribution warehouses, shippers and customers, all factors, which
add to the magnitude of the availability and serviceability predicament.
Anecdotal evidence has revealed
over the years that containers were spotted as unconventional housing
substitute in various developing countries throughout the globe. Not
necessarily the intended use, to the chagrin of the airlines’,
which regularly conduct sweeps to locate missing equipment.
So there you have it – give
the ULD some respect!
Ted Braun
|