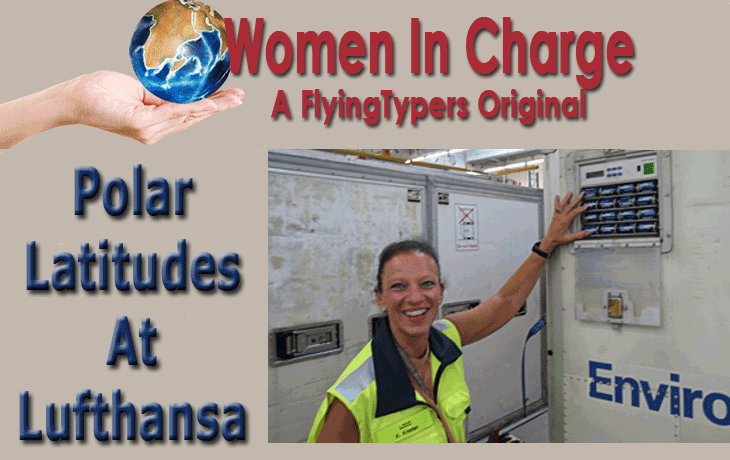
aby,
it’s
cold (and
colder) inside
any one of
four giant
reefer rooms
at The Lufthansa
Cargo Cool
Center at
Frankfurt
International
Airport.
As early January
moves inexorably
toward a winter
rendezvous,
the degrees
of cool that
rule inside
this place
are mirrored
in many parts
of the world
outside as
well.
But
if anyone
is still hot
under the
collar at
what will
be remembered
as a tough
2012, you
would need
to look hard
to see it
in this busy,
giant layout
of container-filled
rooms as each
hums along,
too cool for
school.
Take
the case of
Karin Krestan,
Head of the
Lufthansa
Cargo Cool
Center and
the energetic
and engaging
boss lady
of all things—temperature
sensitive.
Armed
with a keen
working knowledge
of how the
cool-chain
must be handled
and what appears
to be more
D-Cell batteries
than that
pink bunny
could imagine,
Karin Krestan
oversees a
24/7 ballet—moving
everything
from the pharma
and healthcare
business through
giant electric
doors to aircraft
waiting outside
on the ramp.
After
spending an
hour with
this most
professional
lady, we kept
thinking it
was too bad
our refrigerator
at home (the
one with the
six inch rule—meaning
if you consume
something
more than
half a foot’s
reach from
the door,
you’re
on your own)
doesn’t
have someone
with Karin’s
expertise
and sense
of humor to
come in and
do a quick
reboot.
It’s
the age of
the onboard,
self-contained
cooling refrigerated
containers,
from Envirotainer
to Opticooler,
the brilliant
invention
of a local
German company
and Lufthansa
Cargo that
carries its
own electronic
brain and
power pack
to keep temperatures
level at all
times throughout
transit.
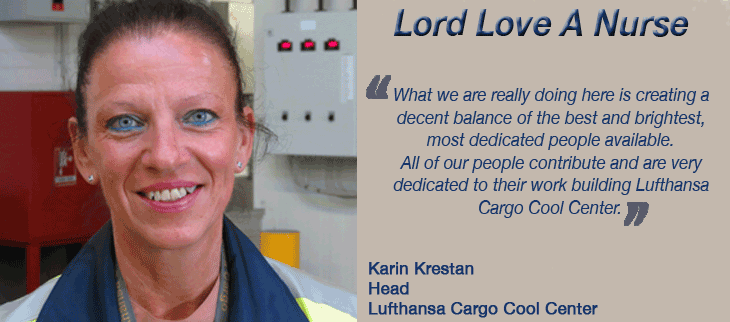 |
“Lufthansa
has a vast
menu of service
offerings
for pharmaceuticals,
diagnostics,
clinical trials,
biotechnological
material as
well as temperature
sensitive
high-tech
products,
including
temperature-controlled
ground storage.
However we
are a ground-up
cool-chain
with appropriate
cooling facilities,
including
our dedicated
Cool Center
operations
here at our
hub, Frankfurt,
and also in
other places
such as Chicago,
Johannesburg
and Bangalore.
“We
offer temperature-ranges
per compartment
onboard the
aircraft and
road feeder
services with
temperature-controlled
reefer trucks.
Our innovative
cool-chain
solutions
include reduction
of transit
points by
operating
via Lufthansa´s
Hubs at Frankfurt,
Munich and
Vienna as
well as a
variety of
containers
that see specific
services,
including
Ice Cooler
for perishables
mainly, Unicooler
and Opticooler
for pharmaceuticals
and high-tech
shipments.
“Lufthansa
Cargo transports
approximately
56,000 tonnes
of temperature
cool/td-shipments
very year.
“Top
routes for
pharmaceuticals
are from South
America to
Europe, Europe
to Asia, and
Europe to
North America.
“The
pharmaceutical
industry is
developing
rapidly and
is a major
focus here
as growth
figures in
the next few
years ahead
are quite
positive.
“Where,
prior to 2012
when this
center opened,
we handled
not only perishables
but also our
Cool/td consignments
at Perishable
Center Frankfurt
(PCF), the
necessity
for the new
pharma-zone
(driven by
capacity limits
at PCF) now
has the consignments
being handled
in our own
dedicated
facility,
offering our
products Cool/td-Active
and Cool/td-Passive
consignments
as well as
temperature
sensitive
Dangerous
Goods at the
best possible
conditions.
“The
Lufthansa
Cargo Cool
Center is
equipped with
state-of-the-art
cool storage
rooms for
four different
temperature
ranges, exclusive
ramps for
delivery and
goods acceptance,
an exclusive
Competence
Center Temperature
Control (CCTC)
supervision
team on call
24/7, and
an exclusive
service provider,
handling:counts.
“Another
advantage
is that our
pharma-zone
coolchain
solution at
Frankfurt
is located
within the
security hub
and has direct
access to
the apron.
“This
guarantees
short distances
and minimizes
cross-transfer
between different
facilities.”
Karin
Krestan began
her career
at Lufthansa
working on
the passenger
side, but
before long
her professional
training as
a medical
nurse took
hold and after
reading about
the Cool Competence
Center some
five years
ago, Karin
was immediately
fascinated
at the possibilities
of bringing
her firsthand
knowledge
of pharma
and vaccines,
plasma etc.
to work, building
the Lufthansa
offering while
still located
at PCF.
“I
discovered
right away
that the pharmaceutical
industry very
much likes
talking to
someone who
has working
knowledge
and understanding
of the medical
arts in such
matters as
temperature
sensitivity
of certain
pharma products:
for example,
how to handle
insulin.”
“We
are quite
accomplished
in our business
here but are
still at work
improving
our offering,
including
product development
and always
refining features
to better
serve our
customers.
“But
it is most
important
that we offer
regularity—i.e.,
staying away
from critical
situations
associated
with any fluctuation
in temperature
for the goods
we move through
here.
“Keeping
things on
a steady beam
requires constant
monitoring,
which we do
at a special
24/7 desk,
and that offers
temperature
monitoring
and mapping.
“We
also hold
meetings that
are conducted
both internally
amongst our
team members
and externally
with our customers
to develop
the best systems
and practices
that interface
via computer
with shippers.
“They
can track
much of the
same information
about their
shipments
that we are
also watching,
including
current conditions
and delivery
schedules.
“This
two-way contact
keeps everybody
on the same
page with
complete transparency
and no surprises.
“We
are also quite
proactive
in getting
the word to
our customers
at once if
a delay or
something
else occurs.”
We
wonder how
Karin first
became a nurse,
recalling
that at one
time back
in the early
1920s, all
flight attendants
serving aboard
line aircraft
in America
were nurses.
This was at
a time when
the ride aboard,
say, a Ford
Tri-Motor
could get
rough enough
to warrant
medical attention.
“I
worked in
the local
hospital in
Darmstadt
as a nurse’s
aide during
my student
years.
“I
just got used
to the work
and liked
the interaction
with the patients,
how the hospital
operated,
and I guess
I never forgot
that time.
“I
spent three
years working
in the Emergency
Room, where
the real action
is.
“Then
a close friend
was hired
as a flight
attendant
at Lufthansa
and I thought
that working
for this airline
would be an
interesting
career.
“But
having just
given birth
to my first
child, working
aboard aircraft
and travelling
would not
have worked,
so I was hired
here to work
on the ramp.
“After
a few years
on the passenger
side, I moved
to the Lufthansa
training center
in Seeheim,
where I then
began teaching
what I had
learned.
“One
of the more
interesting
aspects of
teaching at
Seeheim is
the opportunity
to attend
any of the
classes offered
there, including
training on
how to be
a station
manager for
Lufthansa
anywhere in
the world.
“From
that training
I was able
to work as
a replacement
manager in
some interesting
stations,
including
Kenya and
Russia, before
finally making
my move to
Lufthansa
Cargo as head
of aircraft
handling.
“After
going to air
cargo there
was one more
move to the
passenger
side before
finally advancing
to this opportunity
to go back
to the future,
utilizing
and uniting
my time in
the medical
arts with
my love of
aviation at
Lufthansa.
“So
things have
gone full
circle, but
I really love
this job.
“Five
years ago
when I began
here, my team
included six
men; today
our team includes
six women
plus 15 men.”
We
wonder where
is the equality
in that and
not missing
a beat, Karin
says:
“I’m
working on
it!”
After
the laughter
subsides,
Karin gets
serious and
says:
“What
we are really
doing here
is creating
a decent balance
of the best
and brightest,
most dedicated
people available.
“All
of our people
contribute
and are very
dedicated
to their work
building Lufthansa
Cargo Cool
Center,”
Karin Krestan
said.
As
we leave this
most interesting
part of the
mighty Lufthansa
Cargo combine
at Frankfurt
Airport, a
sticker that
my Mother
used to feature
on the rear
bumper of
her VW Golf
comes to mind:
“Lord
Love A Nurse,”
it said.
Now
that we know
one, we can
understand
why.
Geoffrey |