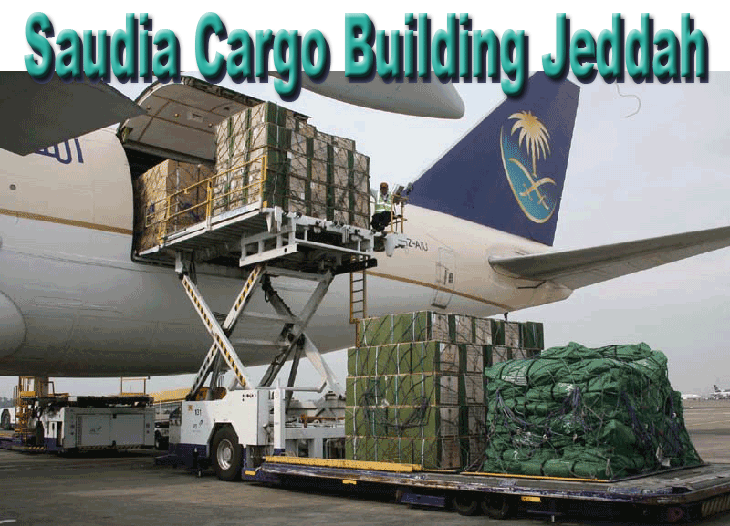
ohammed
Rafie Abdulaziz
Linjawi is Vice
President Cargo
Operations at Saudi
Airlines Cargo Company
(Saudia Cargo).
With over 35 years
of experience in
both the passenger
and cargo sectors
of Saudi Arabian
Airlines, Mr. Linjawi
continues to contribute
his unmatched expertise
and leadership aptitude
towards sustaining
seamless operational
performances within
Saudia Cargo.
His
extensive portfolio
includes various
positions as GM
Industry & Arab,
Station Manager,
GM Pax SVS &
Sales and GM Cargo
& Airmail. Here,
Mr. Linjawi looks
back at the year
that was and what
lies ahead for 2013.
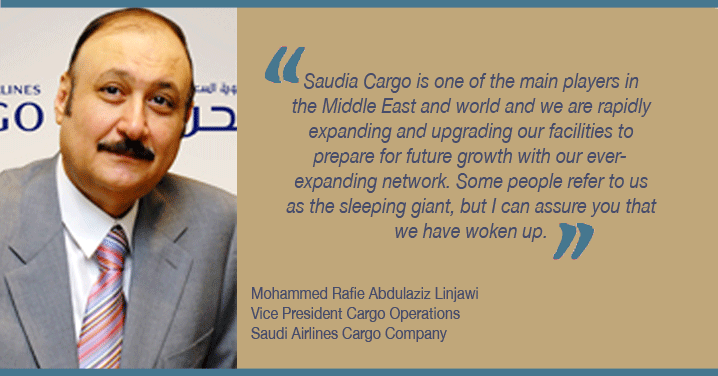 |
“All
main stations in
KSA (Jeddah, Riyadh
and Dammam) have
seen a major increase
in cargo traffic,
especially imports.
In order to deal
with this large
influx of traffic
(25-40 percent),
we are in the process
of upgrading our
facilities, equipment,
and processes to
deal with these
volumes from Saudi
Airlines Cargo Co.
and other airlines.
“Saudia
Cargo is currently
handling all air
cargo products,
apart from express
cargo. With the
upgrade of our facilities,
which started in
2010 and continues
over 2012 and 2013,
Saudia Cargo is
able to handle more
air cargo products
at an even higher
standard.
“We
are in the process
of creating an express
handling area in
our buildings in
RUH, JED, and DMM
in order to deal
with courier/express
cargo from all the
integrators that
operate in Saudi
Arabia. Our cool
facilities are undergoing
an expansion, which
will increase our
capacity for perishables
and other temperature
sensitive products.
Special handling
for Dangerous goods,
high value, live
animals, and environtainers
is already available,”
said Mr. Linjawi.
Based
on its operational
abilities and fortunate
location, there
are many good reasons
why shippers should
take advantage of
Saudia Cargo’s
services. “Saudia
Cargo is perfectly
positioned to handle
both Kingdom originating
and destined cargo
as well as transit
volumes from its
hubs in JED, RUH,
and DMM.
“Saudia
Cargo is capable
of handling all
cargo products in
an efficient and
professional manner.
Our hubs in JED
and RUH are geographically
located to serve
as the gateway to
Africa for transit
cargo from Europe,
the USA, and Asia.
With the upgrade
of our facilities
and ground service
equipment we ensure
smooth and efficient
handling for our
customers,”
said Mr. Linjawi.
With
plans to build a
new cargo center
at JED, one can’t
help but wonder
what new technologies
and systems will
be infused with
the design to help
move Saudia Cargo
further into the
future of cargo
handling capabilities,
especially with
volumes ever on
the rise.
“The
new Cargo Terminal
will be replacing
the current one
on the same site.
Construction will
begin mid 2013 and
is targeted to be
completed in second
quarter 2015. The
plot of land for
the new cargo building
is 600m x 220m.
The building will
be 120m wide and
500m long, and can
be expanded when
necessary in future.
“The
new Cargo Terminal
will handle imports,
exports, and transit
volumes for the
coming 20-30 years.
The
facility will be
designed such that
Saudia Cargo will
be able to expand
quickly to accommodate
ever-growing volumes.
“The
latest cargo handling
systems and designs
are used to create
an efficient flow
of cargo throughput,
with a state-of-the-art
ETV system. All
cargo products will
be catered for and
handled in the most
efficient manner,
with cargo professionals
handling the throughput
in an automated
way. We will have
a special area in
exports, imports
and transit for
temperature-controlled
products.
“The
building will be
designed to handle
all cargo products.
A large perishable
area in both transit
and import will
cater to our forecasted
growth (and beyond).
Express cargo, dangerous
goods, mail, high
value, live animals,
temperature controlled
containers, and
heavy cargo will
all be handled in
separate areas.
The building is
designed to sustain
a large volume increase
in all these products.
“The
facility will be
more than double
the size of our
current one and
will be designed
to expand in the
coming 30 years,
with a modular design.
The new cargo building
will be attractive,
environmentally
friendly, and sustainable,
and equipped with
the latest cargo
handling systems
in order to stimulate
and facilitate cargo-handling
optimization.
“We
are projecting a
throughput between
650,000 and 1 million
tonnes per annum
for 2020-30 and
a short term demand
of 470,000 tonnes
(2015-2020),”
assured Mr. Linjawi.
But
for Saudia Cargo,
it isn’t all
cargo and perishables.
Despite the onward
march of the Internet,
email, and handheld
devices that put
you in touch with
everyone, wherever
you are, there is
still a need for
that simplest of
communiqués—the
mail.
“Mail
is an important
product for Saudia
Cargo (Government
mail, Royal mail,
post office mail)
and we see a steady
growth year on year,
domestic and international.
Between 7-12 percent
of our volumes is
mail (including
newspapers). Mail
volumes are still
growing (domestic
and international),
and are handled
separately in our
facility,”
said Mr. Linjawi.
Saudia
Cargo’s central
location ensures
operation to all
the domestic stations
in the Kingdom;
the main cargo products
handled are “personal
effects, perishables,
mail, newspapers,
and spare parts.”
In
terms of operations
outside the Kingdom,
Mr. Linjawi is very
hands-on and gets
involved in selecting
who operates cargo
in the USA and the
UK.
“We
select handling
agents outside the
Kingdom based on
quality, reputation,
IT capability, and
price. We monitor
their performance
on a daily basis
(on-time performance,
build quality, security,
throughput) and
have a Saudia Cargo
representative at
most stations,”
said Mr. Linjawi.
For
every business operating
in the 21st century,
moving forward must
include a plan for
going green—success
will most definitely
be denied without
it. Of course, Saudia
Cargo is already
thinking about the
environment with
a variety of systems
in place or on the
horizon.
“Saudia
Cargo is committed
to green technology
and practices. Especially
for our new facilities
(as per above),
we will create an
attractive and pleasant
working environment
for the staff and
have optimized handling
processes. For maximizing
the air recirculation,
fresh air supply
will be based on
CO2 metering. There
will be allowance
for free cooling
when outdoor conditions
permit. We will
meter chilled water,
potable water, and
electrical usage.
Pressure drops will
be minimized through
limiting distribution
lengths. Ducting
and pipe work sizing
will be carefully
selected, and energy
saving luminaries
shall be used wherever
possible, with provision
of a comprehensive
lighting control
system. We will
also be using a
grey water system.”
Another
priority for every
operator today is
security, so it
is no surprise that
Saudia has a plan
for that too.
“Air
Cargo Security is
of the utmost priority
to Saudia Cargo.
We are compliant
to all security
regulations and
have facilities
that are monitored
by CCTV cameras
and security staff
24 hours a day.
We have the latest
cargo X-ray/screening
machines in our
facilities compliant
with the FSA regulation.
“Security
has impacted our
operation and we
are complying to
the latest regulation.
We screen all of
our cargo (export
and transit to USA/EU),
and customs in KSA
has a 100 percent
inspection policy
for import cargo.
Our new facilities
will be a fully
controlled and secured
environment with
the latest technology.
Our current facilities
are also fully controlled
and secured,”
said Mr. Linjawi.
For
Saudia Cargo, successful
air cargo operations
are defined by “efficient
handling, short
transit times, secure
environment, integrated
IT systems and a
pleasant environment
for our staff.
“We
have our procedures
and processes. If
those are not respected
or communicated
effectively by our
customers and airlines
that we serve, it
does result in offloads
and misconnectivity.
We regularly invite
our customers and
airlines to visit
our facilities and
discuss the issues
that they might
have. We always
come to a solution
and even adjust
our processes at
times to best serve
our customers.
“Saudia
Cargo is one of
the main players
in the Middle East
and world and we
are rapidly expanding
and upgrading our
facilities to prepare
for future growth
with our ever-expanding
network. Some people
refer to us as the
sleeping giant,
but I can assure
you that we have
woken up,”
said Mr. Linjawi.
Geoffrey/Flossie
|